ใช้กล้องจุลทรรศน์อิเล็กตรอนแบบส่องกราดเพื่อสังเกตการแตกหักของความล้าและวิเคราะห์กลไกการแตกหัก ในเวลาเดียวกัน การทดสอบความล้าแบบหมุนด้วยการหมุนบนชิ้นงานที่แยกคาร์บอนออกที่อุณหภูมิต่างๆ เพื่อเปรียบเทียบอายุการใช้งานความล้าของเหล็กทดสอบที่มีและไม่มีการแยกสลายคาร์บอน และเพื่อวิเคราะห์ผลของการแยกสลายคาร์บอนต่อประสิทธิภาพความล้าของเหล็กทดสอบ ผลการวิจัยพบว่า เนื่องจากการมีอยู่ของออกซิเดชันและดีคาร์บูไรเซชันในกระบวนการทำความร้อนพร้อมกัน ปฏิกิริยาระหว่างทั้งสอง ส่งผลให้ความหนาของชั้นที่แยกคาร์บอนออกจนหมดพร้อมกับการเติบโตของอุณหภูมิแสดงให้เห็นแนวโน้มของการเพิ่มขึ้นแล้วลดลง ความหนาของชั้นที่แยกคาร์บอนออกเต็มที่ถึงค่าสูงสุด 120 μm ที่ 750 ℃ และความหนาของชั้นที่แยกคาร์บอนออกจนหมดถึงค่าต่ำสุด 20 μm ที่ 850 ℃ และขีดจำกัดความล้าของเหล็กทดสอบคือประมาณ 760 MPa และ แหล่งที่มาของรอยแตกเมื่อยล้าในเหล็กทดสอบส่วนใหญ่เป็นสาร Al2O3 ที่ไม่ใช่โลหะ พฤติกรรมการแยกคาร์บอนจะช่วยลดอายุการใช้งานความล้าของเหล็กทดสอบได้อย่างมาก ซึ่งส่งผลต่อประสิทธิภาพความล้าของเหล็กทดสอบ ยิ่งชั้นการแยกคาร์บอนหนาขึ้น อายุความล้าก็จะยิ่งลดลง เพื่อลดผลกระทบของชั้นดีคาร์บูไรเซชันต่อประสิทธิภาพความล้าของเหล็กทดสอบ ควรตั้งอุณหภูมิการรักษาความร้อนที่เหมาะสมของเหล็กทดสอบไว้ที่ 850°C
เกียร์เป็นส่วนประกอบสำคัญของรถยนต์เนื่องจากการทำงานที่ความเร็วสูง ส่วนที่เป็นตาข่ายของพื้นผิวเกียร์จะต้องมีความแข็งแรงและทนต่อการเสียดสีสูง และรากฟันจะต้องมีประสิทธิภาพการล้าในการดัดงอที่ดีเนื่องจากการรับน้ำหนักซ้ำอย่างต่อเนื่อง เพื่อหลีกเลี่ยงรอยแตกที่นำไปสู่วัสดุ การแตกหัก การวิจัยแสดงให้เห็นว่าการแยกชิ้นส่วนเป็นปัจจัยสำคัญที่ส่งผลต่อประสิทธิภาพความล้าของการหมุนด้วยการหมุนของวัสดุโลหะ และประสิทธิภาพความล้าของการหมุนด้วยการหมุนเป็นตัวบ่งชี้ที่สำคัญของคุณภาพของผลิตภัณฑ์ ดังนั้นจึงจำเป็นต้องศึกษาพฤติกรรมการแยกส่วนประกอบของคาร์บอนและประสิทธิภาพความล้าของการหมุนด้วยการหมุนของวัสดุทดสอบ
ในบทความนี้ เตารักษาความร้อนในการทดสอบการแยกคาร์บอนของพื้นผิวเหล็กเกียร์ 20CrMnTi วิเคราะห์อุณหภูมิความร้อนที่แตกต่างกันในความลึกของชั้นการแยกคาร์บอนของเหล็กทดสอบของกฎหมายที่เปลี่ยนแปลง ใช้เครื่องทดสอบความล้าแบบลำแสงธรรมดา QBWP-6000J ในการทดสอบความล้าแบบหมุนด้วยเหล็กทดสอบ การกำหนดประสิทธิภาพความล้าของเหล็กทดสอบ และในเวลาเดียวกันเพื่อวิเคราะห์ผลกระทบของการแยกคาร์บอนต่อประสิทธิภาพความล้าของเหล็กทดสอบสำหรับการผลิตจริงเพื่อปรับปรุง กระบวนการผลิต ยกระดับคุณภาพของผลิตภัณฑ์ และจัดให้มีการอ้างอิงที่สมเหตุสมผล ประสิทธิภาพความล้าของเหล็กทดสอบถูกกำหนดโดยเครื่องทดสอบความล้าแบบหมุนดัด
1. วัสดุและวิธีการทดสอบ
วัสดุทดสอบสำหรับยูนิตเพื่อจัดหาเหล็กเกียร์ 20CrMnTi ซึ่งเป็นองค์ประกอบทางเคมีหลักดังแสดงในตารางที่ 1 การทดสอบการแยกคาร์บอน: วัสดุทดสอบถูกประมวลผลเป็นชิ้นงานทรงกระบอก Ф8 มม. × 12 มม. พื้นผิวควรมีความสว่างโดยไม่มีคราบ เตาบำบัดความร้อนได้รับความร้อนที่ 675 ℃, 700 ℃, 725 ℃, 750 ℃, 800 ℃, 850 ℃, 900 ℃, 950 ℃, 1,000 ℃ ลงในชิ้นงานทดสอบและค้างไว้ 1 ชั่วโมง จากนั้นจึงระบายความร้อนด้วยอากาศจนถึงอุณหภูมิห้อง หลังจากการอบชุบชิ้นงานด้วยความร้อนโดยการตั้งค่า การเจียร และขัดเงา โดยการกัดกร่อนของสารละลายกรดไนตริกแอลกอฮอล์ 4% การใช้กล้องจุลทรรศน์โลหะวิทยาเพื่อสังเกตชั้นการแยกคาร์บอนของเหล็กทดสอบ วัดความลึกของชั้นการแยกคาร์บอนที่อุณหภูมิต่างกัน การทดสอบความล้าแบบหมุนด้วยการหมุน: วัสดุทดสอบตามความต้องการของการประมวลผลของตัวอย่างความล้าแบบหมุนด้วยการหมุนสองกลุ่ม กลุ่มแรกไม่ได้ทำการทดสอบการแยกส่วน ส่วนกลุ่มที่สองของการทดสอบการแยกส่วนที่อุณหภูมิต่างกัน การใช้เครื่องทดสอบความล้าแบบหมุนด้วยการหมุน เหล็กกล้าทดสอบทั้งสองกลุ่มสำหรับการทดสอบความล้าแบบหมุนด้วยการหมุน การกำหนดขีดจำกัดความล้าของเหล็กทดสอบทั้งสองกลุ่ม การเปรียบเทียบอายุการใช้งานความล้าของเหล็กทดสอบทั้งสองกลุ่ม การใช้การสแกน การสังเกตการแตกหักของความล้าด้วยกล้องจุลทรรศน์อิเล็กตรอนวิเคราะห์สาเหตุของการแตกหักของชิ้นงานเพื่อสำรวจผลกระทบของการแยกส่วนประกอบของคุณสมบัติความล้าของเหล็กทดสอบ
ตารางที่ 1 องค์ประกอบทางเคมี (เศษส่วนมวล) ของเหล็กทดสอบ wt %
ผลของอุณหภูมิความร้อนต่อการแยกคาร์บอน
สัณฐานวิทยาขององค์กรการแยกสลายคาร์บอนภายใต้อุณหภูมิความร้อนที่แตกต่างกันจะแสดงในรูปที่ 1 ดังที่เห็นได้จากภาพ เมื่ออุณหภูมิอยู่ที่ 675 ℃ พื้นผิวตัวอย่างจะไม่ปรากฏชั้นการแยกสลายคาร์บอน เมื่ออุณหภูมิสูงขึ้นถึง 700 ℃ ชั้นการแยกส่วนประกอบของพื้นผิวตัวอย่างเริ่มปรากฏขึ้น สำหรับชั้นการแยกส่วนประกอบของเฟอร์ไรต์บาง ๆ เมื่ออุณหภูมิสูงขึ้นถึง 725 ℃ ความหนาของชั้นการแยกคาร์บอนของพื้นผิวตัวอย่างเพิ่มขึ้นอย่างมีนัยสำคัญ ความหนาของชั้น decarburization 750 ℃ถึงค่าสูงสุด ในเวลานี้ เม็ดเฟอร์ไรต์มีความชัดเจนมากขึ้น หยาบ; เมื่ออุณหภูมิสูงขึ้นถึง 800 ℃ ความหนาของชั้นการแยกคาร์บอนเริ่มลดลงอย่างมีนัยสำคัญ ความหนาลดลงเหลือครึ่งหนึ่งของ 750 ℃; เมื่ออุณหภูมิยังคงเพิ่มขึ้นถึง 850 ℃ และความหนาของการแยกคาร์บอนไดออกไซด์จะแสดงในรูปที่ 1 800 ℃ ความหนาของชั้นการแยกคาร์บอนเต็มเริ่มลดลงอย่างมีนัยสำคัญ ความหนาของมันลดลงเหลือ 750 ℃ เมื่อครึ่งหนึ่ง เมื่ออุณหภูมิยังคงเพิ่มขึ้นถึง 850 ℃ขึ้นไป ความหนาของชั้นการแยกคาร์บอนของเหล็กทดสอบยังคงลดลง ความหนาของชั้นการแยกคาร์บอนครึ่งหนึ่งเริ่มค่อยๆ เพิ่มขึ้นจนกระทั่งสัณฐานวิทยาของชั้นการแยกคาร์บอนเต็มหายไปทั้งหมด สัณฐานวิทยาของชั้นการแยกคาร์บอนครึ่งหนึ่งค่อยๆ ชัดเจน จะเห็นได้ว่าความหนาของชั้นที่แยกคาร์บอนออกเต็มที่โดยมีอุณหภูมิเพิ่มขึ้นในตอนแรกแล้วจึงลดลง สาเหตุของปรากฏการณ์นี้เกิดจากการที่ตัวอย่างอยู่ในกระบวนการให้ความร้อนในเวลาเดียวกันกับพฤติกรรมการเกิดออกซิเดชันและการแยกคาร์บอนเฉพาะเมื่อ อัตราการสลายตัวจะเร็วกว่าความเร็วของการเกิดออกซิเดชันจะปรากฏเป็นปรากฏการณ์การสลายตัว ที่จุดเริ่มต้นของการให้ความร้อน ความหนาของชั้นที่แยกคาร์บอนออกจนหมดจะเพิ่มขึ้นทีละน้อยตามอุณหภูมิที่เพิ่มขึ้นจนกระทั่งความหนาของชั้นที่แยกคาร์บอนออกจนหมดถึงค่าสูงสุด ในเวลานี้เพื่อเพิ่มอุณหภูมิต่อไป อัตราการเกิดออกซิเดชันของชิ้นงานจะเร็วกว่า อัตราการแยกสลายคาร์บอนซึ่งจะไปยับยั้งการเพิ่มขึ้นของชั้นสลายคาร์บอนจนหมดส่งผลให้มีแนวโน้มลดลง จะเห็นได้ว่าภายในช่วง 675 ~ 950 ℃ ค่าความหนาของชั้นที่แยกคาร์บอนออกเต็มที่ที่ 750 ℃ นั้นมีค่ามากที่สุด และค่าความหนาของชั้นที่แยกคาร์บอนออกเต็มที่ที่ 850 ℃ นั้นน้อยที่สุด ดังนั้นอุณหภูมิความร้อนของเหล็กทดสอบจึงแนะนำให้อยู่ที่ 850 ℃
รูปที่ 1 จุลสัณฐานวิทยาของชั้นสลายคาร์บอนของเหล็กทดสอบที่ถูกจับที่อุณหภูมิความร้อนต่างกันเป็นเวลา 1 ชั่วโมง
เมื่อเปรียบเทียบกับชั้นกึ่งแยกคาร์บอนแล้ว ความหนาของชั้นที่แยกคาร์บอนออกทั้งหมดมีผลกระทบด้านลบที่รุนแรงมากขึ้นต่อคุณสมบัติของวัสดุ ซึ่งจะช่วยลดคุณสมบัติทางกลของวัสดุได้อย่างมาก เช่น ลดความแข็งแรง ความแข็ง ความต้านทานการสึกหรอ และขีดจำกัดความเมื่อยล้า ฯลฯ และยังเพิ่มความไวต่อการแตกร้าว ส่งผลต่อคุณภาพการเชื่อม เป็นต้น ดังนั้นการควบคุมความหนาของชั้นที่แยกคาร์บอนออกอย่างสมบูรณ์จึงมีความสำคัญอย่างยิ่งในการปรับปรุงประสิทธิภาพของผลิตภัณฑ์ รูปที่ 2 แสดงเส้นโค้งการเปลี่ยนแปลงของความหนาของชั้นที่แยกคาร์บอนออกเต็มที่ตามอุณหภูมิ ซึ่งแสดงให้เห็นการเปลี่ยนแปลงของความหนาของชั้นที่แยกคาร์บอนออกเต็มที่ได้ชัดเจนยิ่งขึ้น จากรูปจะเห็นได้ว่าความหนาของชั้นที่แยกคาร์บอนออกทั้งหมดอยู่ที่ประมาณ 34μm ที่ 700°C; เมื่ออุณหภูมิสูงขึ้นถึง 725 ℃ ความหนาของชั้นที่แยกคาร์บอนออกเต็มที่จะเพิ่มขึ้นอย่างมากเป็น 86 μm ซึ่งมากกว่าสองเท่าของความหนาของชั้นที่แยกคาร์บอนออกเต็มที่ที่ 700 ℃; เมื่ออุณหภูมิสูงขึ้นเป็น 750 ℃ ความหนาของชั้นที่แยกคาร์บอนออกจนหมด เมื่ออุณหภูมิสูงขึ้นถึง 750 ℃ ความหนาของชั้นที่แยกคาร์บอนออกจนหมดจะมีค่าสูงสุด 120 μm เมื่ออุณหภูมิยังคงสูงขึ้น ความหนาของชั้นที่แยกคาร์บอนออกทั้งหมดจะเริ่มลดลงอย่างรวดเร็วเป็น 70 μm ที่ 800 ℃ และจากนั้นก็เหลือค่าต่ำสุดประมาณ 20 μm ที่ 850 ℃
รูปที่ 2 ความหนาของชั้นที่แยกคาร์บอนออกเต็มที่ที่อุณหภูมิต่างๆ
ผลของการสลายคาร์บอนต่อประสิทธิภาพความล้าในการดัดแบบสปิน
เพื่อศึกษาผลกระทบของการแยกส่วนประกอบออกจากคาร์บอนต่อคุณสมบัติความล้าของเหล็กสปริง ได้ทำการทดสอบความล้าจากการดัดด้วยสปินดัดสองกลุ่ม กลุ่มแรกคือการทดสอบความล้าโดยตรงโดยไม่มีการแยกส่วนประกอบออกจากคาร์บอน และกลุ่มที่สองคือการทดสอบความล้าหลังการแยกคาร์บอนด้วยความเครียดเดียวกัน ระดับ (810 MPa) และกระบวนการแยกคาร์บอนถูกจัดขึ้นที่ 700-850 ℃ เป็นเวลา 1 ชั่วโมง ชิ้นงานทดสอบกลุ่มแรกแสดงอยู่ในตารางที่ 2 ซึ่งเป็นอายุความล้าของเหล็กสปริง
อายุการใช้งานความล้าของชิ้นงานทดสอบกลุ่มแรกแสดงอยู่ในตารางที่ 2 ดังที่เห็นได้จากตารางที่ 2 หากปราศจากการแยกคาร์บอน เหล็กทดสอบจะถูกทดสอบเพียง 107 รอบที่ 810 MPa และไม่มีการแตกหักเกิดขึ้น เมื่อระดับความเครียดเกิน 830 MPa ตัวอย่างบางส่วนเริ่มแตกหัก เมื่อระดับความเครียดเกิน 850 MPa ชิ้นงานทดสอบความล้าจะแตกหักทั้งหมด
ตารางที่ 2 ชีวิตความเหนื่อยล้าภายใต้ระดับความเครียดต่างๆ (โดยไม่มีการแยกคาร์บอน)
เพื่อกำหนดขีดจำกัดความล้า จะใช้วิธีกลุ่มเพื่อกำหนดขีดจำกัดความล้าของเหล็กทดสอบ และหลังจากการวิเคราะห์ข้อมูลทางสถิติ ขีดจำกัดความล้าของเหล็กทดสอบจะอยู่ที่ประมาณ 760 MPa เพื่อระบุลักษณะอายุการใช้งานความล้าของเหล็กทดสอบภายใต้ความเค้นที่แตกต่างกัน กราฟ SN จะถูกพล็อต ดังแสดงในรูปที่ 3 ดังที่เห็นได้จากรูปที่ 3 ระดับความเครียดที่แตกต่างกันจะสอดคล้องกับอายุความล้าที่แตกต่างกัน เมื่ออายุความล้าที่ 7 ซึ่งสอดคล้องกับจำนวนรอบสำหรับ 107 ซึ่งหมายความว่าชิ้นงานภายใต้สภาวะเหล่านี้จะผ่านสถานะ ค่าความเค้นที่สอดคล้องกันสามารถประมาณได้เป็นค่าความล้าซึ่งก็คือ 760 MPa จะเห็นได้ว่าเส้นโค้ง S - N มีความสำคัญต่อการกำหนดอายุความล้าของวัสดุซึ่งมีค่าอ้างอิงที่สำคัญ
รูปที่ 3 เส้นโค้ง SN ของการทดสอบความล้าแบบหมุนด้วยเหล็กทดลอง
อายุความล้าของชิ้นงานทดสอบกลุ่มที่สองแสดงอยู่ในตารางที่ 3 ดังที่เห็นได้จากตารางที่ 3 หลังจากที่เหล็กทดสอบถูกแยกส่วนประกอบออกจากคาร์บอนที่อุณหภูมิต่างกัน จำนวนรอบจะลดลงอย่างเห็นได้ชัด และมีค่ามากกว่า 107 และทั้งหมด ชิ้นงานทดสอบความล้าแตกหัก และอายุความล้าลดลงอย่างมาก เมื่อรวมกับความหนาของชั้น decarburized ข้างต้นกับเส้นโค้งการเปลี่ยนแปลงของอุณหภูมิที่สามารถมองเห็นได้ ความหนาของชั้น decarburized 750 ℃จะใหญ่ที่สุดซึ่งสอดคล้องกับค่าต่ำสุดของชีวิตความเมื่อยล้า ความหนาของชั้น decarburized 850 ℃มีขนาดเล็กที่สุด ซึ่งสอดคล้องกับค่าชีวิตความเมื่อยล้าค่อนข้างสูง จะเห็นได้ว่าพฤติกรรมการแยกสลายคาร์บอนจะช่วยลดประสิทธิภาพความล้าของวัสดุได้อย่างมาก และยิ่งชั้นสลายคาร์บอนหนาขึ้น อายุความล้าก็จะยิ่งลดลง
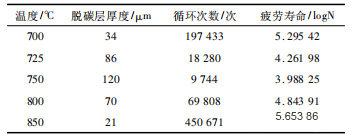
ตารางที่ 3 อายุการใช้งานของความล้าที่อุณหภูมิการแยกคาร์บอนต่างกัน (560 MPa)
สัณฐานวิทยาการแตกหักของความเมื่อยล้าของชิ้นงานทดสอบด้วยกล้องจุลทรรศน์อิเล็กตรอนแบบส่องกราด ดังแสดงในรูปที่ 4 รูปที่ 4(a) สำหรับพื้นที่แหล่งกำเนิดรอยแตก สามารถมองเห็นรูปส่วนโค้งของความล้าได้ชัดเจน ตามส่วนโค้งของความล้าเพื่อค้นหาแหล่งที่มา ของความเมื่อยล้า สามารถมองเห็นได้ แหล่งที่มาของรอยแตกสำหรับการรวมอโลหะ "ตาปลา" การรวมที่ความเข้มข้นของความเครียดที่ง่ายต่อการก่อให้เกิด ส่งผลให้เกิดรอยแตกเมื่อยล้า; รูปที่ 4(b) สำหรับสัณฐานวิทยาของพื้นที่ส่วนขยายของรอยแตกร้าว สามารถมองเห็นแถบความล้าได้ชัดเจน มีการกระจายเหมือนแม่น้ำ เป็นของการแตกหักแบบกึ่งแยกส่วน โดยมีรอยแตกขยายออก และนำไปสู่การแตกหักในที่สุด รูปที่ 4(b) แสดงสัณฐานวิทยาของพื้นที่การขยายตัวของรอยแตกร้าว มองเห็นริ้วรอยความล้าที่เห็นได้ชัดเจน ในรูปแบบของการกระจายเหมือนแม่น้ำ ซึ่งเป็นการแตกหักแบบกึ่งแยกตัว และด้วยการขยายตัวของรอยแตกอย่างต่อเนื่อง จนนำไปสู่การแตกหักในที่สุด .
การวิเคราะห์การแตกหักของความล้า
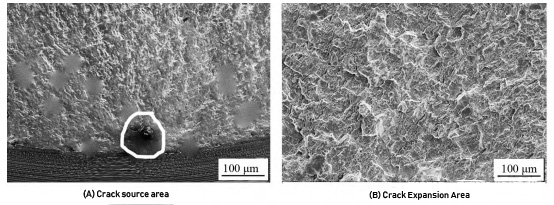
รูปที่ 4 สัณฐานวิทยา SEM ของพื้นผิวแตกหักเมื่อยล้าของเหล็กทดลอง
เพื่อกำหนดประเภทของการรวมในรูปที่ 4 การวิเคราะห์องค์ประกอบสเปกตรัมพลังงานได้ดำเนินการ และผลลัพธ์จะแสดงในรูปที่ 5 จะเห็นได้ว่าการรวมที่ไม่ใช่โลหะส่วนใหญ่เป็นการรวม Al2O3 ซึ่งบ่งชี้ว่าการรวม เป็นสาเหตุหลักของรอยแตกร้าวที่เกิดจากการแตกร้าวแบบรวม
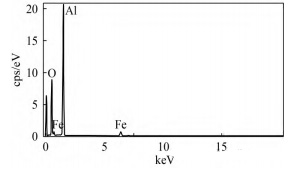
รูปที่ 5 สเปคโทรสโกปีพลังงานของการรวมอโลหะ
สรุป
(1) การวางตำแหน่งอุณหภูมิความร้อนที่ 850 ℃ จะลดความหนาของชั้นที่แยกคาร์บอนออกให้เหลือน้อยที่สุด เพื่อลดผลกระทบต่อประสิทธิภาพความล้า
(2) ขีดจำกัดความล้าของการดัดสปินของเหล็กทดสอบคือ 760 MPa
(3) การทดสอบการแตกร้าวของเหล็กในวัสดุที่ไม่ใช่โลหะ ซึ่งส่วนใหญ่เป็นส่วนผสมของ Al2O3
(4) การแยกคาร์บอนออกช่วยลดอายุความล้าของเหล็กทดสอบอย่างจริงจัง ยิ่งชั้นการแยกคาร์บอนหนาขึ้น อายุความล้าก็จะยิ่งลดลง
เวลาโพสต์: 21 มิ.ย.-2024